At Lion Paper, delivering premium quality stationery products is at the heart of everything we do. As one of the most reliable global manufacturers of notebooks, planners, calendars, and other stationery essentials, we know that quality assurance isn't just a step in our production—it's our promise to customers.
To ensure every product we ship meets our stringent quality standards, we've developed a detailed, transparent, and systematic quality inspection process. In this comprehensive guide, we walk you through each meticulous step our professional inspectors follow to guarantee customer satisfaction and maintain our exceptional brand reputation.
1. Appearance Inspection
Ensuring flawless visual appeal
Our inspection begins with a thorough evaluation of each product's appearance. Inspectors meticulously check the surfaces of our stationery items to ensure they are pristine, free of stains, scratches, or deformations. The printed covers are examined carefully to confirm the uniformity of colors and clarity of texts—no blurring or ghosting is tolerated.
Furthermore, inspectors evaluate the quality of inner pages, searching diligently for creases, tears, or missing prints. Products are precisely measured using standardized rulers to verify they meet the exact specifications outlined in customer orders.
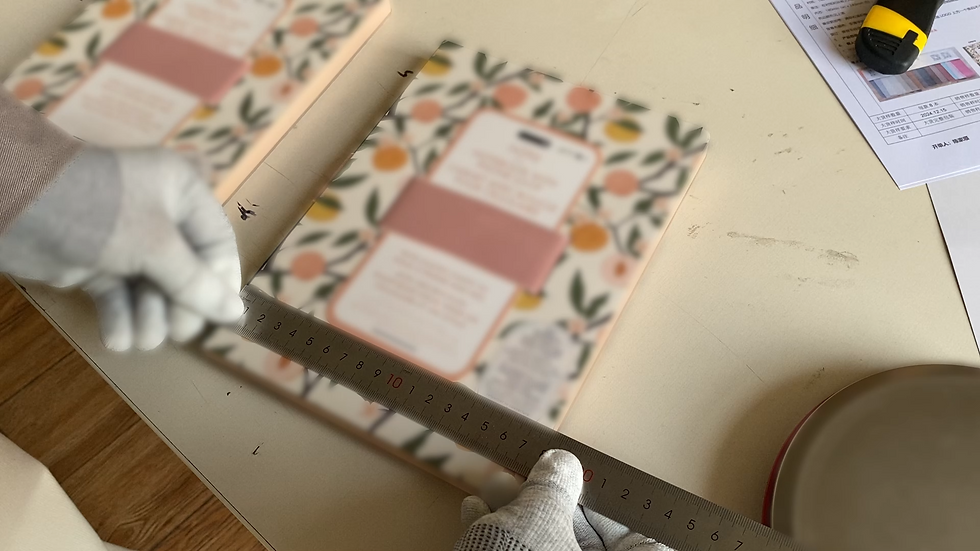
2. Paper Quality Inspection
Delivering a superior writing experience
Paper quality is integral to our products. Inspectors begin by feeling each paper's texture, ensuring smoothness and appropriate thickness align with our high standards. We perform comprehensive writing tests with different types of pens—ballpoint, gel, and marker pens—to guarantee that our paper resists ink bleeding and feathering.
Additionally, inspectors execute a page-turning test, confirming each page moves smoothly without sticking, ensuring the customer's writing experience remains pleasant and frustration-free.

3. Binding Quality Inspection
Durable construction for lasting use
Our binding inspection process addresses the distinct requirements of each binding type:
Spiral-bound notebooks: Inspectors confirm spirals are intact, aligned precisely, and without breaks or looseness.
Glued-bound notebooks: We validate the durability of the glued spine and ensure covers are adhered properly without potential peeling.
Sewn-bound notebooks: Our team verifies stitches are evenly spaced and securely sewn, without any loose threads.
Inspectors further conduct a shake test, gently shaking notebooks to confirm no components are loose, reinforcing product integrity.

4. Printing Color Inspection
Accurate color representation
Color accuracy is crucial to uphold our branding consistency and meet customer expectations. Our inspectors leverage Pantone Color Guides for precise color matching, guaranteeing any color deviations fall within acceptable limits.
Print alignment is also scrutinized carefully. Inspectors ensure texts and graphics are perfectly aligned without skewing or misprints. Attention to detail means graphics edges remain sharp, and no text is omitted or incorrectly printed.
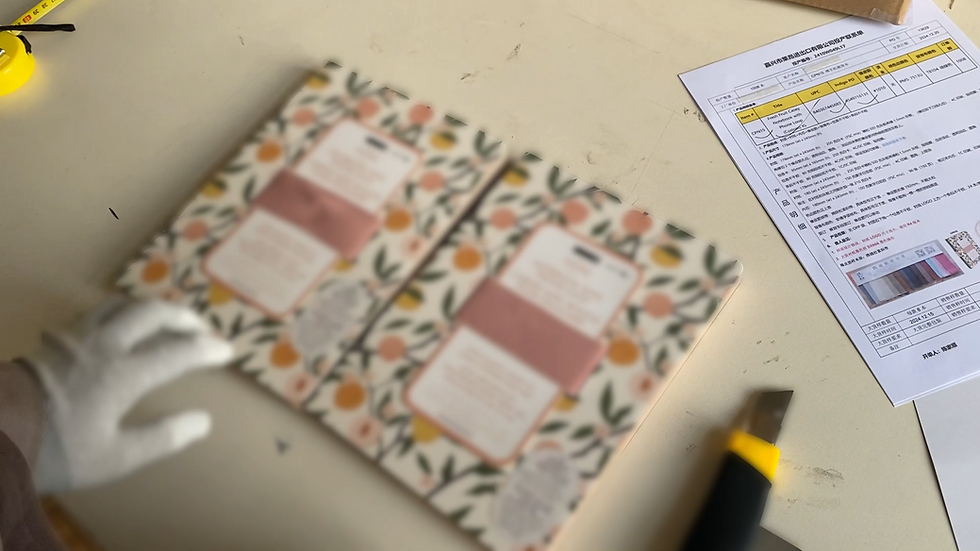
5. Page Layout & Pagination Check
Precision and consistency in every page
Inconsistent pagination and misprints negatively affect customer perception. Inspectors randomly flip through products to catch any missing, duplicated, or incorrect pages. They meticulously ensure the correct sequential order of page numbers.
Text layout undergoes rigorous evaluation, confirming consistent alignment without shifts, double printing, or misplaced text. This attention ensures the functionality and usability of our stationery products.

6. Weight-bearing Test
Reliability under pressure
Transportation can be demanding on stationery items. Thus, we simulate transportation pressure through our weight-bearing tests. Multiple products are stacked, and pressure is systematically applied to identify any potential deformities or damages.
Inspectors use specialized pressure tools or apply manual pressure directly. Products are confirmed resilient, exhibiting no creasing, warping, or cracking under normal transit conditions, ensuring arrival in perfect condition.
7. Packaging Inspection
Protecting your products
Proper packaging safeguards products from potential shipping hazards. Our inspectors assess packaging integrity thoroughly, ensuring outer boxes show no signs of damage or deformation.
Inside, protective materials are evaluated to ensure products remain secured and protected throughout transit. Packaging labels and barcodes—including SKU, batch numbers, and customer information—are carefully verified for accuracy. Compression tests ensure packaging durability, offering reliable protection during transportation.

8. Inspection Body Camera for Transparency
Building trust through transparency
Transparency is a key differentiator at Lion Paper. Our inspectors use body cameras during quality checks, capturing critical steps like page checks, binding verification, and packaging accuracy.
These recorded inspection processes are uploaded securely to our cloud storage, providing customers real-time access to quality control activities. This practice significantly enhances transparency, accountability, and customer trust.

9. Final Approval & Shipment
The final seal of quality assurance
Upon completing all prior steps, inspectors compile detailed quality reports for supervisor review. Once validated, products proceed to shipment. Packaging is carefully sealed, and a QC Passed sticker visibly affirms quality approval.
Products are then handed to our logistics team for efficient, secure delivery, ensuring your products arrive punctually and in impeccable condition.

Summary
Lion Paper's quality inspection process is intentionally rigorous and methodical, meticulously covering appearance, paper quality, binding durability, printing precision, page accuracy, transport resilience, packaging robustness, and full transparency through inspection recordings.
This comprehensive quality assurance strategy doesn't merely reduce return rates—it significantly enhances our brand's reputation by instilling confidence in our global customer base. When you partner with Lion Paper, you partner with excellence, transparency, and reliability—every single time.
Leo Xia
CEO, Lion Paper Products
“You design, we deliver.”
Kommentarer